Fluorinated gases have a potent greenhouse effect and are widely used as refrigerants. Especially HFC (hydrofluorocarbons) are very much used in refrigerating technologies, and are to be phased out. Yet, they still cause a major problem to the environment and speed up climate change.
This is the reason why the phasing out HFC for a couple of years was the number one solution in the Project Drawdown Table of the 100 most effective solutions to keep on track of the Paris Agreement. Refrigerant management is still on top of the list from the nonprofit organisation that is one of the world’s leading resources for climate solutions.
Project Drawdown presents the most effective solutions to reach “drawdown” – the point in the future when levels of greenhouse gases in the atmosphere stop climbing and start to steadily decline, thereby stopping climate change.
Furthermore, all their solutions to stop global warming exist today. You might be surprised to see just how much can be done in refrigerant management – without even replacing the existing refrigeration, air-conditioning and heat pump (RACHP) equipment.
Almost any workplace has refrigerators, air condition, and heat pumps. Much medicine needs to be in cold storage as well. Therefore, we find it appropriate to have a look at the super effective and super simple solutions in this area.
A briefing note from the United Nations Environment Programme presents six solutions right at hand:
- Minimising the cooling load.
- Minimising the temperature lift.
- Accounting for variable operating conditions.
- Selecting the most efficient refrigeration cycle and components.
- Design of effective control systems.
- Checking operating performance and correcting any faults of existing RACHP systems
Project Drawdown
Project Drawdown's mission is to help the world reach “drawdown”—the point in the future when levels of greenhouse gases in the atmosphere stop climbing and start to steadily decline, thereby stopping catastrophic climate change—as quickly, safely, and equitably as possible.
Read more about Project Drawdown.
1. Minimising the cooling load
There are many examples of RACHP equipment cooling an unnecessary load. You might have noticed the refrigerators in supermarkets with no doors, like the bottle coolers for instance. It would seem odd to remove the door of your fridge at home, and it is. Just by putting doors in the refrigerators, 60 percent of energy can be saved.
Another opportunity is to use “free-cooling” to pre-cool a hot product prior to using refrigeration. For example, a cooked product in a food factory at close to 100°C is often cooled with refrigeration. The cooling load can sometimes be reduced by over 50 percent by pre-cooling the product with ambient air or water cooled in a cooling tower.
2. Minimising the temperature lift
RACHP system efficiency is very sensitive to the temperature lift. Even a few degrees Celsius can make a big difference. A refrigeration system collects unwanted heat at a low temperature and transfers that heat into the ambient surroundings at a higher temperature. Energy consumption depends on the temperature lift between the product being cooled and the ambient – with a bigger temperature lift, more energy must be used.
Just a 1-degree Celsius extra temperature lift will add 2 to 4 percent to the energy used by a plant. Through poor design or poor plant operation it is easy to accidentally add an extra 10 or 15 degrees Celsius to the temperature lift – that could add 20 to 40 percent to the total energy consumption.
Therefore, it is important to minimise the temperature lift of an RACHP system by making the “cold end” (called “the evaporator”) stay at the highest possible temperature, and the “hot end” (called “the condenser”) at the lowest possible temperature.
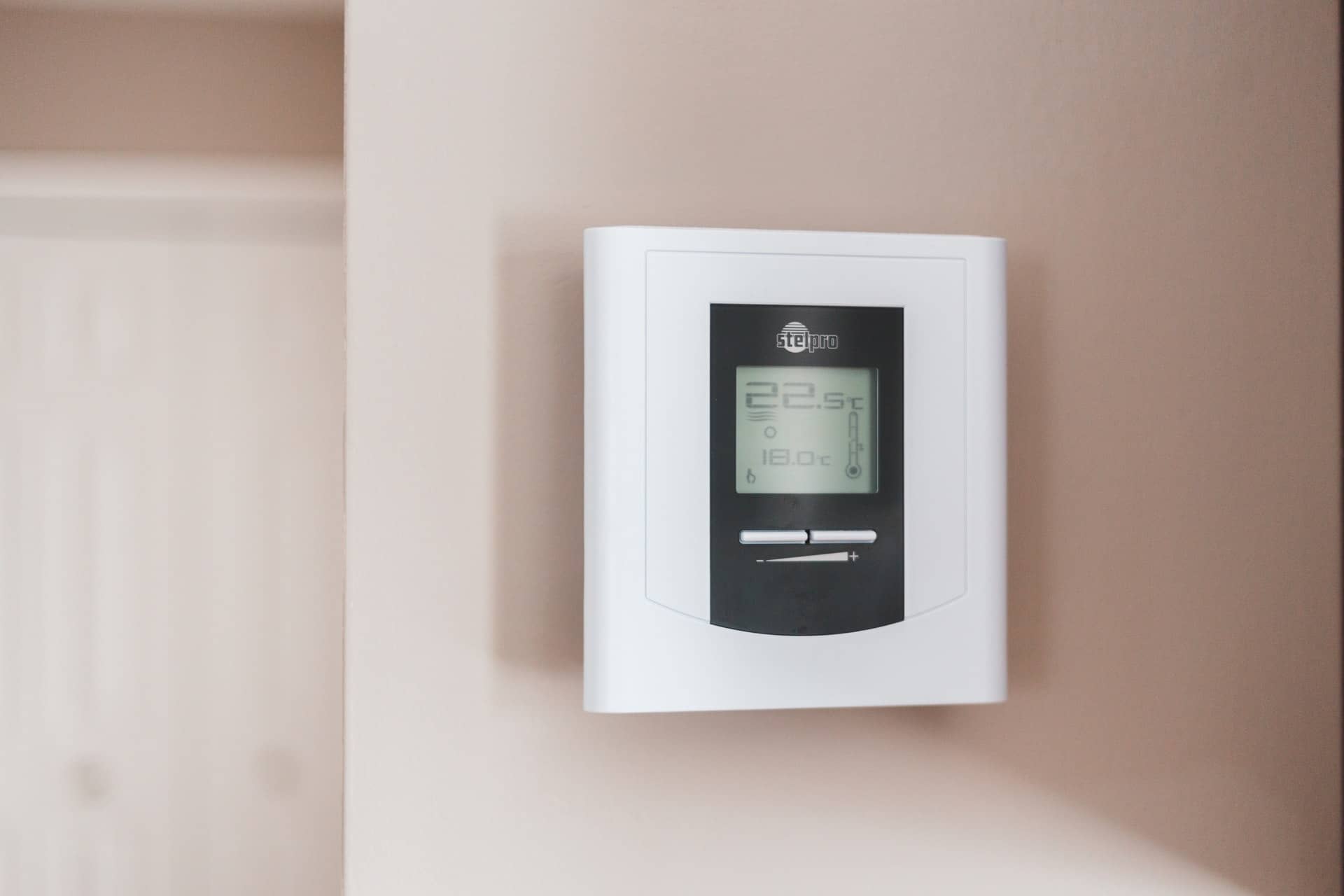
3. Accounting for variable operating conditions
Many RACHP systems are designed and optimised for operation at the “design point”. But very few RACHP systems operate at their peak load “design point” (for instance, maximum cooling load under hottest possible ambient temperature) for many hours of the year. RACHP equipment usually spends the majority of time operating at part load and at ambient temperatures well below the peak.
Operation can be very inefficient if these off-design conditions were not considered when the plant was designed. One example is to replace one single large chiller with a high cooling capacity with four smaller chillers to improve the overall operating efficiency. In one specific case the overall operating efficiency improved by 25 percent, and the extra investment for buying the smaller chillers had a payback period of less than two years.
UN Briefing Note
Read the full text from the United Nations Environment Programme: Briefing Note B. The Potential to Improve the Energy Efficiency of Refrigeration, Air-conditioning and Heat Pumps.
4. Selecting the most efficient refrigeration cycle and components
Cooling equipment is complex, consisting of numerous components. There have been many recent advances in the efficiency of individual components such as compressors and heat exchangers and in the efficiency of advanced refrigeration cycles. Each component needs to be optimised for maximum energy efficiency for the intended application.
The main electricity using component of any RACHP system is the compressor. Two almost identical compressors, with the same capital cost, could have energy efficiencies that differ by more than 20 percent – with no extra capital cost. Therefore, there is a great business case for simply selecting the best compressor for the expected operating conditions.
5. Design of effective control systems
One of the biggest opportunities to improve RACHP energy efficiency relates to control. Many older systems have very poor control systems that do not optimise control to ensure maximum energy efficiency. Instead, many inefficient systems use a crude form of “on-off” control to achieve the required temperature. Use of a variable speed compressor improves the accuracy of temperature control and makes a significant efficiency improvement.
Many refrigeration plants are fitted with a head pressure control (HPC) system. An HPC can be very wasteful if it is set at an incorrect pressure level. Annual savings can be more than 25 percent. In some cases, these savings are achieved with no capital investment, by simply adjusting HPC settings.
6. Checking operating performance and correcting any faults of existing RACHP systems
It is very common that RACHP systems develop faults that reduce efficiency. It is important to monitor performance and to recognise when a fault has developed, especially on medium and large sized cooling systems. Refrigerant leakage leads to undercharging of a system and is one example of many different operating faults that can create a significant loss of efficiency.
Many RACHP systems operate for years with control or maintenance related problems that go undetected. It is really important that performance is regularly measured. If energy use is creeping up there could be a maintenance issue that can quickly be resolved. Unfortunately, it is common to find that savings of 10 to 20 percent that are not achieved, due to the lack of monitoring the performance of an existing system and correcting any faults identified.
Next step
As the UN briefing note shows, there are a wide range of technical measures that can be adopted to improve the energy efficiency of RACHP equipment. The refrigerant must be selected with care, but refrigerant choice should be recognised as only having a relatively small impact on efficiency.
Other design issues listed above have a much greater impact on efficiency than refrigerant choice. By maximizing efficiency, you are lowering negative impact on climate change.
References
- United Nations Environment Programme: Briefing Note B. The Potential to Improve the Energy Efficiency of Refrigeration, Air-conditioning and Heat Pumps. Link: https://ozone.unep.org/sites/default/files/2019-08/briefingnote-b_potential-to-improve-the-energy-efficiency-of-refrigeration-air-conditioning-and-heat-pumps.pdf
- Project Drawdown: https://drawdown.org/